L'histoire d'une feuille de papier : La technologie du papier
La fabrication du papier comporte deux étapes principales: la formation de la pâte, c’est-à-dire la dissociation des éléments du bois et la séparation des fibres individuelles; la transformation de la pâte en feuille dans une machine à papier.
Du bois à la pâte à papier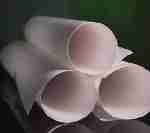
La partie supérieure de la figure 168 résume la transformation du bois en pâte à papier et les traitements que cette dernière subit avant d’être transformée en feuille de papier.
L’obtention des pâtes
Cette opération, appelée défibrage, consiste à séparer les fibres, c’est-à-dire toutes les cellules du bois, en modifiant le moins possible leurs caractéristiques morphologiques et chimiques. Selon les types de papier désirés, on peut utiliser des procédés différents, mécanique, chimique, recyclage.
La voie mécanique. Les pâtes mécaniques sont faites de bois simplement râpé ou broyé. On part en général de rondins ou de copeaux. Après écorçage, les billes de bois sont pressées contre une meule abrasive travaillant dans l’eau ou triturées entre les disques défibreurs d’un raffineur.
L’imprégnation par l’eau des rondins et la chaleur dégagée contribuent à ramollir les lignines qui cimentent les fibres au niveau des lamelles moyennes. Les fibres sont en quelque sorte arrachées au matériau soit individuellement, soit en paquets, soit encore en bûchettes. Le rendement est très élevé, de l’ordre de 90 à 95%, ce qui signifie que presque toute la matière première est transformée en pâte, y compris la presque totalité des lignines. Lorsqu’on observe cette pâte au microscope photonique après une coloration des lignines, il est facile d’y reconnaître les cellules du bois, trachéides et fibres, souvent coupées par le traitement et encore largement incrustées de lignine. Dans le langage papetier, ces pâtes sont souvent appelées «pâtes à bois» dans la mesure où elles contiennent encore un fort pourcentage de lignines.
Les pâtes mécaniques sont largement utilisées pour la fabrication des journaux, des magazines, des intérieurs de cartons, c’est-à-dire des papiers opaques qui ne seront pas conservés très longtemps. En effet, ils résistent mal au vieillissement, devenant rapidement jaunes et cassants du fait de la photosensibilité des groupements phénoliques des lignines. Des pâtes mécaniques peuvent être utilisées en partie pour l’obtention de papiers à usage graphique auxquels elles apportent l’opacité.
La voie chimique. Le but des traitements chimiques est d’éliminer les composés autres que la cellulose, et plus particulièrement les lignines et les résines. En termes de papeterie, on parle alors de « pâtes sans bois ». Ce procédé est très développé dans les régions septentrionales de l’Europe (Finlande, Suède) et en Amérique, où se sont implantées de nombreuses usines de pâte à papier.
Les bois sont écorcés, déchiquetés en petits copeaux de quelques centimètres maximum. Ils sont mis à cuire dans un réacteur chimique appelé « lessiveur ». La cuisson se fait à haute température (entre 130 et 180 °C), sous pression, pendant plusieurs heures. Le rendement est plus faible que pour les pâtes mécaniques : de 45 à 55% à cause de l’élimination des lignines
et autres constituants. Deux procédés de lessivage sont couramment utilisés : alcalin ou acide.
Le procédé alcalin, ou procédé au sulfate, est souvent appelé « procédé Kraft» (de l’allemand et du suédois kraft, «force»). Il est très largement employé aussi bien à partir de résineux que de feuillus. L’agent de cuisson est une solution de soude (NaOH), dont l’action est désincrustante, et de sulfure de sodium (Na2S), qui sert de réserve de soude. Au cours de la cuisson, des composés soufrés volatils s’échappent dans l’atmosphère, les mercaptans, d’odeur nauséabonde et de toxicité non négligeable.
La pâte liquide qui sort du lessiveur est lavée plusieurs fois et séparée de la liqueur alcaline. La liqueur résiduaire, très foncée, appelée « liqueur noire», contient les lignines, les hémicelluloses et les résines dans le cas des résineux. Cette liqueur subit un traitement pour séparer les matières organiques des agents chimiques. Ces derniers sont récupérés et donnent la liqueur blanche, mélange de soude et de sulfure de sodium régénérés, que l’on peut introduire dans le lessiveur pour une autre cuisson. En fin de cuisson, la pâte obtenue est dite « pâte écrue ». Elle est de couleur brune ou grisée. La pâte kraft a une très bonne résistance mécanique et peut être utilisée directement pour la fabrication des emballages. Souvent, elle est soumise à un traitement de blanchiment. On parle alors de « pâte blanchie » qui entre dans la composition de nombreux papiers pour l’impression- écriture et l’emballage. Avec ce procédé, les fibres obtenues sont largement désincrustées de leurs lignines. On reconnaît les éléments conducteurs et les fibres, généralement assez homogènes et rigides, aux parois fortement biréfringentes et aux lumières cellulaires (lumen) plus ou moins étroites. Peu de fibres apparaissent coupées.
Le procédé acide, ou procédé au bisulfite, utilise une liqueur à base d’acide sulfureux. Il est employé surtout pour des bois de résineux. L’élément chimique actif est l’anhydride sulfureux (S02) libre ou combiné. Les lignines sont transformées en acides ligno-sulfoniques solubles qui peuvent être ainsi éliminés.
L’un des problèmes les plus importants liés à ce type de fabrication est celui de l’évacuation des liqueurs résiduaires, c’est-à-dire des solutions ligno-sulfoniques issues des lessiveurs. Longtemps déversées dans les rivières, pratique aujourd’hui interdite, elles doivent subir de nouveaux traitements. La pâte issue de ce procédé est moins résistante que la pâte mécanique et sert le plus souvent à fabriquer du papier de qualité pour l’écriture. L’observation au microscope de ces pâtes montre des trachéides plus souples que dans les pâtes kraft.
Il existe d’autres procédés de fabrication des pâtes. On distingue les procédés mi-chimiques, qui combinent un traitement chimique pour enlever les composés non cellulosiques du bois et un traitement mécanique pour disperser les fibres. Les pâtes obtenues ont des caractéristiques intermédiaires: leur qualité est supérieure à celles des pâtes mécaniques et le rendement est plus grand que celui des procédés chimiques. On distingue aussi les procédés thermo-mécaniques dans lesquels les copeaux sont traités avant défibrage par un étuvage à la vapeur (température supérieure à 100 °C). Le début du défibrage est également effectué sous pression. Dans ces pâtes, les fibres sont moins endommagées que dans les pâtes purement mécaniques; elles apparaissent longues et homogènes, mais restent très riches en lignines.
Le recyclage
Les pâtes mécaniques et chimiques sont parfois appelées «pâtes vierges» dans la mesure où elles sont fabriquées à partir d’un matériau vierge, le bois.
La « pâte recyclée » est au contraire fabriquée à partir de papiers et de cartons ayant subi un premier usage. On parle ainsi couramment de FCR, fibres cellulosiques de récupération (un autre sigle est parfois utilisé, PCR, papiers et cartons récupérés). Ces fibres proviennent soit des circuits industriels (rognures d’imprimerie, emballages, journaux invendus…), soit des circuits ménagers (emballages, journaux, magazines…). Elles constituent actuellement une source de matière première très importante, autour de 58 % en France.
Les fibres récupérées sont d’abord défibrées, c’est-à-dire remises en suspension par remouillage et brassées dans un pulpeur. Ensuite, on procède à l’élimination des contaminants non utilisables: élimination des agrafes avec des aimants, des matières plastiques, des cerclages métalliques par triturage, élimination des colles par lavage et éventuellement des encres par désencrage. Ce dernier se fait grâce à une action mécanique et à l’utilisation d’une mousse de savon créatrice de bulles: ces bulles se fixent sur les particules d’encre et montent en flottaison en surface où elles sont récupérées. Les fibres recyclées servent principalement à la fabrication de papiers d’emballage.
Le blanchiment des pâtes
Comme on vient de le voir, les pâtes obtenues selon les différents procédés sont plus ou moins claires, les plus foncées restant toujours les pâtes mécaniques. La plupart du temps un blanchiment est nécessaire pour des raisons esthétiques, mais aussi pour améliorer la qualité du papier (résistance à la rupture, au vieillissement). On définit un degré de blancheur en ISO, exprimé en pourcentage : un degré de blancheur de 100% ISO correspond au corps le plus blanc connu, c’est-à-dire à l’oxyde de magnésium, qui réfléchit 100 % de la lumière. Là encore, il existe plusieurs procédés de blanchiment selon les pâtes utilisées.
Les pâtes mécaniques écrues. Elles peuvent être éclaircies par un traitement oxydant à l’hypochlorite de sodium (assez rare) et le plus souvent à l’eau oxygénée (H202). La réaction est la suivante :
H202^ OOH-+ H+
Les ions OOH~ oxydent les groupements chromophores phénoliques des lignines. Les lignines ne sont pas extraites, elles sont seulement « décolorées ». Le degré de blancheur est de l’ordre de 80 % ISO. C’est une méthode peu coûteuse, mais le blanchiment obtenu n’est pas stable. Le papier fabriqué à partir de ces pâtes jaunit plus ou moins vite, en particulier sous l’action de la lumière comme c’est souvent le cas de nombreux journaux. On peut aussi blanchir les pâtes mécaniques par réduction avec de l’hydrosulfite de sodium à 60 °C et à pH 5 (le pH exprime la concentration en ions H+ d’une solution). Le degré de blancheur obtenu est de l’ordre de 70% ISO. Quelquefois, on peut aussi coupler l’action d’un agent oxydant et d’un agent réducteur.
Les pâtes chimiques. Elles sont blanchies par un traitement complexe dont le but est d’éliminer les lignines résiduelles. La pâte est mise dans un « mixeur » avec des réactifs dont l’action est séquentielle et prolongée. Les agents de blanchiment des pâtes chimiques sont nombreux: le chlore, le dioxyde de chlore, l’hypochlorite de sodium, l’eau oxygénée, l’oxygène, l’ozone. Selon les exigences de la fabrication, on procède à des séquences de blanchiment différentes désignées par des sigles chez les papetiers : C pour le traitement au dichlore (Cl2); D pour le traitement au dioxyde de chlore (CI02) ; H pour le traitement à l’hypochlorite de sodium (NaCIO ou eau de Javel) ; P pour le traitement au peroxyde d’hydrogène (H202 ou eau oxygénée) ; O pour le traitement par le dioxygène (02) ; E pour les étapes d’extraction alcaline à chaud. Par exemple, pour une pâte écrue de type kraft blanchie au chlore, on utilise souvent la séquence C E D E D en cinq stades :
– l’étape C est une chloration par le dichlore, qui permet de dégrader les lignines résiduelles et conduit à la formation de chloro-lignines solubles dans la soude ;
– l’étape E est une extraction alcaline à chaud, pour solubiliser les chloro- lignines dégradées;
– les étapes D E D suivantes permettent d’obtenir la pâte blanchie par action du dioxyde de chlore sur les phénols de la lignine résiduelle. Celle- ci est solubilisée et extraite.
Pour les pâtes au bisulfite, le blanchiment est plus facile et la séquence peut être plus courte : C E H pour chloration, extraction alcaline puis traitement à l’hypochlorite de sodium. Les pâtes peuvent alors atteindre un degré de blancheur de 92 % ISO. Quand on les regarde au microscope photonique, on y reconnaît les éléments cellulaires déjà décrits, mais le test des lignines montre effectivement que les lignines ont disparu.
Ces opérations de blanchiment coûtent cher et sont relativement polluantes, un grand pourcentage du chlore utilisé se transformant en composés organochlorés rejetés dans les eaux. Cela pose des problèmes considérables en termes d’environnement. Ainsi, on estime que pour 450 g de pâte kraft écrue issue de 1 kg de bois, on obtient 420 g de pâte blanche et 30 g d’effluents chlorés qu’il faudra traiter en station d’épuration. L’élimination totale du chlore (pâte TCF, pour total chlorine free, littéralement « papier zéro chlore ») est actuellement le but recherché par de nombreux industriels.
D’autres séquences de blanchiment ont été mises au point pour remplacer le dichlore, par l’ozone par exemple. Toutefois, l’ozone ayant une action néfaste sur la cellulose, le papier est de moins bonne qualité et ce procédé n’est pas toujours retenu. Les problèmes économiques et environnementaux posés par ces techniques de blanchiment sont évoqués. Après toutes ces étapes, les pâtes peuvent être directement utilisées pour la fabrication de la feuille de papier. On parle alors d’usines intégrées. Le plus souvent, elles sont séchées et compactées en plaques ou en flocons. Elles sont transportées et vendues sous forme de balles aux usines de papier.
Le raffinage
Avant d’entrer dans la machine à papier, la pâte (ou le mélange de pâtes) doit encore subir une préparation. La première opération consiste à désagréger la pâte en la remettant en suspension dans l’eau. Cette opération se fait dans des pulpeurs. L’eau, en se fixant en couche monomoléculaire, puis en couches multiples, écarte les chaînes des régions amorphes des microfibrilles de cellulose. La fibre gonfle et perd une partie de sa rigidité.
La fibre portant de nombreux groupements hydrophiles au niveau de la cellulose a une grande affinité avec l’eau et on obtient ainsi une supension. Après cette désagrégation dans le pulpeur, la pâte subit le raffinage proprement dit. Il s’agit d’une action mécanique sur les fibres en milieu aqueux. Elle se fait dans des raffineurs, appareils à disques tournants entre lesquels s’écoule la suspension fibreuse. Pendant cette opération, où la pâte est triturée énergiquement, l’hydratation se poursuit et, surtout, le phénomène de fibrillation se produit .La paroi primaire mince des fibres, déjà dégradée par la cuisson, est désagrégée. Des éléments fins, nommés «fibrilles», se détachent de la paroi secondaire, augmentant la surface des fibres. Ainsi, les points de contact sont multipliés, et l’enchevêtrement ultérieur des fibres est favorisé.
Des ajouts éventuels
Souvent des produits auxiliaires, les adjuvants, sont introduits dans la pâte après le raffinage, dans le but d’améliorer les propriétés du papier et éventuellement d’abaisser son coût. Ces adjuvants, non fibreux, se fixent sur les fibres hydratées. Les adjuvants sont de plusieurs types :
– des charges minérales, préparées à partir de matières premières plus ou moins élaborées et ajoutées sous forme de poudres fines. On utilise le plus souvent lekaolin (Al203), sorte d’argile blanche, en raison de son coût très faible. On utilise aussi l’oxyde de titane (Ti02), le talc, un silicate naturel de magnésium (3MgO, 4Si02, H20), le gypse (CaS04) et la craie (CaC03). La quantité des charges peut varier de 5 à 30 % par rapport aux fibres sèches. Leur rôle est d’améliorer l’opacité, l’inertie et l’aptitude au lissage des feuilles, ainsi que leur imprimabilité. En revanche, comme elles peuvent affaiblir la résistance mécanique du papier en réduisant le nombre de liaisons directes entre les fibres, elles ne sont donc pas toujours utilisées ;
– des agents de collage ayant pour but de faire adhérer les particules entre elles et de limiter la pénétration de l’eau dans la feuille. Le collage n’est pas le même selon que l’on veut obtenir du papier d’emballage ou du papier d’impression-écriture. Dans ce dernier cas, le collage permet l’écriture manuelle avec des encres aqueuses. Pendant cette étape, on ajoute à la suspension fibreuse une substance ayant une partie hydrophile qui se fixe aux fibres et une partie hydrophobe qui bloque la pénétration de l’eau. On utilise souvent la colophane, ou «gemme», résine naturelle riche en acide abiétique, tirée du pin maritime. On utilise aussi des résines synthétiques de type urée-formol ou mélamine-formol ;
– beaucoup d’autres composés peuvent être incorporés en petite quantité dans la pâte. C’est le cas de l’amidon, souvent utilisé pour accroître la cohésion interne, en favorisant l’établissement de liaisons supplémentaires entre les fibres. La solidité du papier est ainsi renforcée. L’amidon est facilement dissous dans la suspension fibreuse; et au fur et à mesure que la quantité d’eau diminue au cours des différentes étapes, il contribue à établir des liaisons cellulose-amidon-cellulose, donc à rapprocher les fibres Des galactomannanes, des alginates, du galactose, de la carboxyméthyl cellulose ou de la gélatine servent souvent à augmenter la résistance à certains solvants. On utilise aussi des composés cationiques (par exemple des résines polyamidiques) dont le rôle est d’augmenter la rétention des charges. On peut ajouter aussi des azureurs optiques, corps synthétiques utilisés à très faibles doses pour accroître la blancheur du papier;
– des colorants sont fréquemment incorporés à la pâte dans le but d’obtenir des papiers colorés: des colorants basiques (bleu de méthylène, vert malachite, auramine…), des colorants acides (jaune de métanile, bleu soluble, rocceline…), des colorants directs tels la chrysophénine ;
– enfin, citons les composés bactéricides et fongicides permettant d’éviter le développement de microbes sur les papiers.
Les mêmes produits peuvent être utilisés lors d’étapes ultérieures. Au terme de tous ces traitements, on obtient une pâte engraissée, d’aspect laiteux, qui va pouvoir entrer dans la machine à papier. Elle contient des fibres-ou des morceaux défibrés, plus ou moins agglomérés- dans une très grande quantité d’eau.
Vidéo : L’histoire d’une feuille de papier : La technologie du papier
Vidéo démonstrative pour tout savoir sur : L’histoire d’une feuille de papier : La technologie du papier