L'histoire d'une feuille de papier : De la pâte à papier à la feuille
De la pâte à papier à la feuille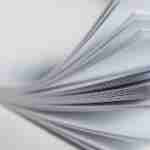
Il s’agit d’opérations inverses de celles réalisées dans l’usine de pâte à papier. Toute l’énergie est consacrée à rapprocher les fibres individualisées. Les opérations se passent dans la machine à papier, une construction très complexe qui va permettre d’extraire l’eau de la pâte, de remettre les fibres en contact intime et d’établir de nombreuses liaisons. Cette machine comprend deux zones : une zone humide où est constitué le matelas fibreux; une zone sèche où sont effectuées les opérations de pressage et de séchage indispensables à la formation de la feuille.
La zone humide. La pâte est amenée par jet dans le cuvier de tête de la machine, grand réservoir de forme variable. À ce niveau, elle est très diluée, contenant entre 97 et 99 % d’eau, soit 1 à 3 % de matière sèche. La face antérieure du réservoir est percée d’une fente qui permet à la pâte liquide de s’écouler sur l’élément suivant : la table de fabrication. f- Il s’agit d’une toile métallique sans fin, tendue entre des rouleaux, et qui défile en continu. La pâte se répartit sur toute la largeur utile de cette table (4 à 10 m).
Sous la table de fabrication sont disposées des caisses aspirantes et des rouleaux égoutteurs, appelés « pontuseaux », qui absorbent une certaine proportion d’eau et permettent un début d’égouttage. Les fibres les plus grosses et les plus longues sont les premières à être déposées sur la toile, au début préférentiellement dans le sens du mouvement, parallèles à l’axe de la machine. Puis, les fibres fines et courtes se déposent de façon plus désordonnée, assurant le colmatage. Le matelas fibreux ainsi formé est donc dissymétrique. Le côté inférieur, appelé « côté toile », contient de grosses fibres relativement orientées, donnant un aspect assez rugueux; le côté supérieur, ou « côté feutre », contient des fibres plus petites et désordonnées, donnant à cette face un aspect plus uni. Pendant cette opération, la toile est souvent soumise à des mouvements saccadés latéraux de façon à éviter une orientation trop uniforme des fibres dans le sens de la «marche» et à favoriser au contraire leur enchevêtrement. Le matelas fibreux formé contient alors entre 75 et 90% d’eau. Il est déjà cohérent. Il est ensuite dirigé, par un feutre coucheur, vers des cylindres de presse au niveau desquels une grande quantité d’eau est encore éliminée. La feuille de papier contient alors de 33 à 45 % d’eau. Sa siccité (pourcentage de matière sèche par rapport au poids de la feuille) a largement augmenté.
Cette opération se fait dans une calandre constituée de rouleaux en fonte trempée, alternés avec des rouleaux élastiques. C’est le microglissement entre les rouleaux, agissant par compression et friction, qui permet de satiner la surface du papier et d’obtenir des papiers plus unis et plus brillants.
Le papier obtenu, dont la surface est égalisée, passe ensuite sur une enrouleuse. Les bobines mères (celles obtenues à la sortie des machines) sont très volumineuses et pèsent plusieurs tonnes. Ensuite, selon les utilisations ultérieures, les bobines sont dirigées vers d’autres industries de transformation.
Les traitements postérieurs
L’apprêt physique précédemment décrit améliore la surface du papier, mais cette amélioration n’est pas parfaite. Il est souvent nécessaire de pratiquer un couchage du papier. Ensuite vient la phase de finition.
Le couchage. Il s’agit du dépôt d’un revêtement externe, sur l’une ou sur les deux faces du support, dans le but d’éliminer les dernières irrégularités et d’obtenir une surface unie. Le couchage réduit la porosité du papier, c’est-à-dire les espaces ménagés entre les fibres lors du dépôt du matelas (la taille moyenne des pores passe de quelques micromètres à quelques dixièmes de micromètres) : il améliore la blancheur et le toucher du papier et permet ensuite une bonne écriture. La plupart des papiers d’impression- écriture sont couchés. Une sauce de couchage est utilisée, c’est-à-dire un enduit qui comprend deux types d’éléments : des pigments constituant la charge minérale (de 80 à 92 %) et un adhésif ou liant (de 8 à 20 %).
Les pigments sont souvent les mêmes matières que celles incorporées dans la pâte au moment de la fabrication du papier comme adjuvants. Ils doivent toutefois, pour cette étape, être plus fins et plus propres. Pour obtenir la blancheur du papier, le kaolin est le plus employé, car il est abondant, facile à utiliser et bon marché. On peut avoir recours aussi au carbonate de calcium précipité et éventuellement au blanc satin, un pigment composite.
L’adhésif a pour rôle de faire adhérer les particules de pigment entre elles mais aussi sur le support. On emploie souvent de l’amidon (de maïs, de blé) ou de la caséine extraite du lait de vache, sous forme de caséinate. Des adhésifs synthétiques sont aussi utilisés: des latex, caoutchoucs de type styrène butadiène ou acrylo-vinylique.
Le couchage se fait dans des ateliers appelés «cuisines». Les opérations sont maintenant automatisées et programmées dans des installations de couchage, appelées « coucheuses ». En plus de ces deux produits de base, pigment et adhésif, il faut souvent ajouter des produits auxiliaires pour donner à la sauce de couchage des qualités encore plus performantes. Aussi utilise-t-on des dispersants, des modificateurs de viscosité (épaississants, fluidifiants), des produits améliorant la rétention d’eau, des insolubilisants, des bactéricides et des fongicides, des colorants ou des azurants optiques. À la fin de ces étapes, on obtient un papier couché dont l’enduction de surface peut varier en épaisseur (de 20 à 30 grammes par mètre carré et par face pour les couchés « classiques », de 5 à 8 g.rrr2 et par face pour les couchés « légers ».
La finition. Elle est différente selon que l’on veut obtenir du «papier en bobines » ou du « papier au format ». Pour du papier en bobines, la finition se fait grâce à des bobineuses. Les bobines mères sont tronçonnées en bobines filles par des couteaux circulaires. Après cette refente, les bobines filles obtenues sont emballées dans du papier kraft ou du papier hydro- fugé (macule) pour distribution. Les bobines sont définies par deux dimensions: leur laize (ou largeur) et leur diamètre. Pour obtenir du papier au format, les bobines sont coupées et mises en feuilles, lesquelles sont empilées et équerrées. Le papier au format, défini par sa longueur et sa largeur, est ensuite conditionné en rames de 500 feuilles, elles-mêmes empilées en palettes. Les différents formats traditionnels et actuels sont donnés.
Les causes physico-chimiques de la solidité du papier
Parmi toutes les étapes de la fabrication d’une feuille de papier, le fait le plus marquant est le passage de la pâte, c’est-à-dire d’une suspension (contenant 97 à 99 % d’eau et 1 à 3 % de matière sèche), au matelas fibreux, c’est-à-dire un réseau composé de fibres liées, d’air et d’une faible quantité d’eau (5 à 10 %, eau Interstitielle ou eau de composition). En fait, le papier a une structure en couches superposées, les fibres étant disposées les unes au-dessus des autres dans diverses directions. Par exemple, un papier d’impression-écriture de 60 g.rrr2 a une épaisseur de 70 à 1oo um et contient dix couches de fibres. Un centimètre carré de ce papier contient environ 10 000 fibres de longueur comprise entre 0,5 et 3,5 pm.
La solidité du papier se traduit par sa capacité de résistance à des contraintes variées (pression, écrasement, cisaillement, tension) qui dépendent toutes de l’usage prévu pour ce papier. Deux facteurs sont déterminants pour établir cette solidité: l’enchevêtrement mécanique et la liaison fibre à fibre qui s’établit lors du retrait de l’eau pendant le dépôt des fibres du matelas fibreux (fig. 180, page suivante). Les liaisons sont principalement des liaisons hydrogène (H) qui s’établissent entre les groupements hydroxyles (OH) à la surface des molécules de cellulose hydratées. Le raffinage, quand il a lieu, favorise aussi l’établissement de ces liaisons. Dans toutes ces étapes, l’eau (ou un autre liquide polaire) est un facteur important pour fournir des liaisons H. On peut le vérifier en utilisant un solvant apolaire (par exemple, le tétrachlorure de carbone): les liaisons fibre à fibre ne se font pas et le papier obtenu n’a aucune solidité.
Vidéo : L’histoire d’une feuille de papier : De la pâte à papier à la feuille
Vidéo démonstrative pour tout savoir sur : L’histoire d’une feuille de papier : De la pâte à papier à la feuille